
Understanding Key USP RegulationsDespite major advancements in healthcare patient safety from hazardous drugs (HD), a lack of enforcement for healthcare staff handling these hazardous drugs remains. Pharmacy compounding is a complicated and detailed department to design, and it becomes even more complicated when hazardous drugs are involved. While there are many practices and quality standards of regulatory entities that compounding facilities must adhere to, such as infection control, State Board of Pharmacy, AHCA, OSHA, and FDA, this article will focus on USP Chapters.
USP Chapter 800, titled "Hazardous Drugs-Handling in Healthcare Settings" is the newest pharmacy document that is dedicated solely to the handling of hazardous drugs within a compounding pharmacy for patient and staff safety and environmental protection. It is the first document to do so and is current as of December 2019. The other USP Chapters (795 and 797) have largely focused on sterile and non-sterile compounding non-HD items while barely touching on the topic of staff handling HD. All three of these chapters include many pharmacy terms and processes that designers may not fully comprehend, which often leaves a lot to designer interpretation.
Is Your Compounding Pharmacy Compliant?
Understanding Key USP RegulationsDespite major advancements in healthcare patient safety from hazardous drugs (HD), a lack of enforcement for healthcare staff handling these hazardous drugs remains. Pharmacy compounding is a complicated and detailed department to design, and it becomes even more complicated when hazardous drugs are involved. While there are many practices and quality standards of regulatory entities that compounding facilities must adhere to, such as infection control, State Board of Pharmacy, AHCA, OSHA, and FDA, this article will focus on USP Chapters.
USP Chapter 800, titled "Hazardous Drugs-Handling in Healthcare Settings" is the newest pharmacy document that is dedicated solely to the handling of hazardous drugs within a compounding pharmacy for patient and staff safety and environmental protection. It is the first document to do so and is current as of December 2019. The other USP Chapters (795 and 797) have largely focused on sterile and non-sterile compounding non-HD items while barely touching on the topic of staff handling HD. All three of these chapters include many pharmacy terms and processes that designers may not fully comprehend, which often leaves a lot to designer interpretation.
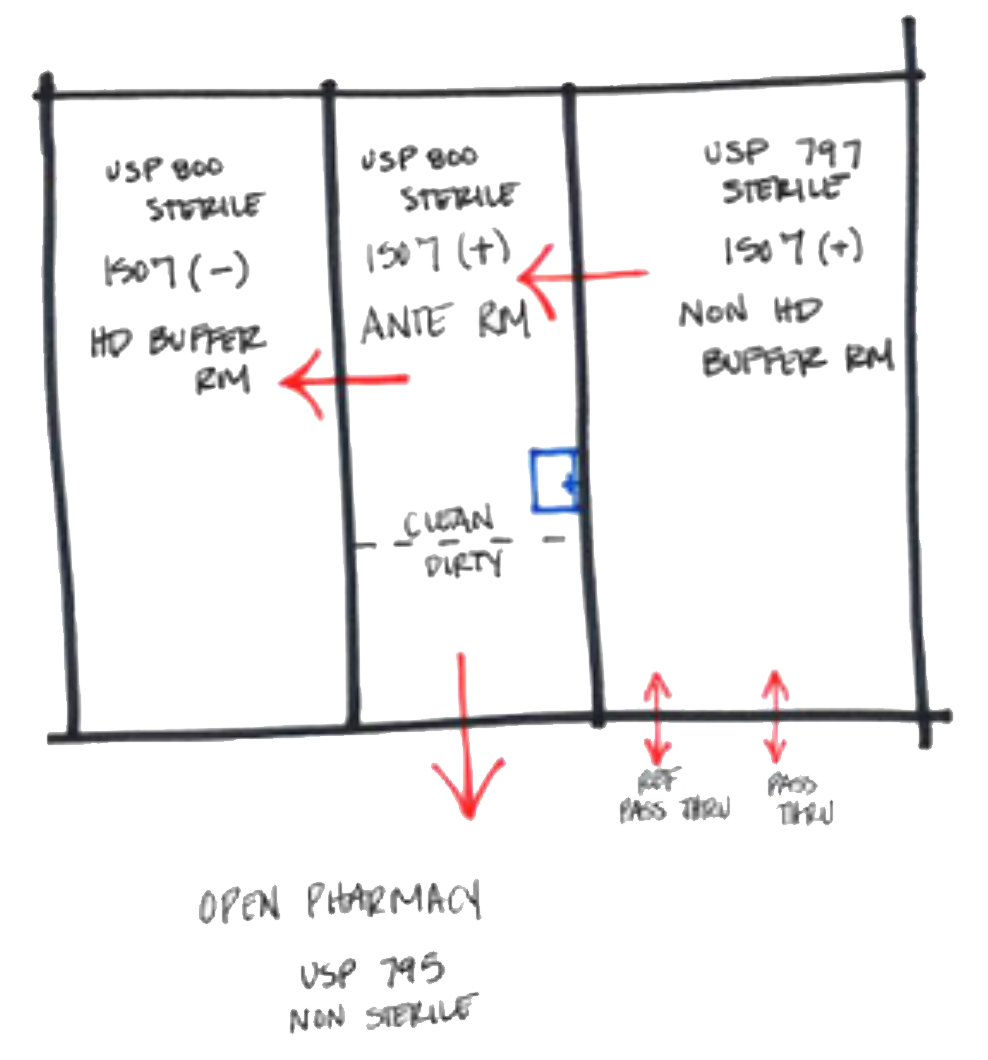
Examples of healthcare facilities that will utilize these chapters the most (especially USP 800) are cancer treatment facilities and full-service hospitals. Ambulatory surgery centers and certain physicians' offices also may have some type of compounding on-site. Most existing and compliant USP 795/797 facilities that handle HD preparations will have to make updates to become compliant with USP 800. These updates could include HVAC changes, operational changes, and additional enclosed or segregated rooms. These facility types represent one major focus of Flad's healthcare work.
As architects, we must remember that USP 800 is not intended to replace USP Chapters 795 and 797, but rather to be used in conjunction with them. Since USP 800 was developed, there are four aspects of compounding activities: USP 800 Sterile HD, USP 800 Nonsterile HD, USP 797 Sterile Non-HD, and USP 795 Nonsterile Non-HD. Planners should not simply read the facilities and engineering controls section of the chapters; they should read the entire chapters that address all processes, including staffing and operational procedures. Knowing all operational processes will help planners understand how to design the space more efficiently and effectively.
Staff Flow and ProcessAs an architectural associate with interest in healthcare planning, I have found that the most challenging aspect of planning a hospital-based compounding pharmacy is understanding the specific client's staff and material flows and operational processes. The key to a successful layout is not just to follow the USP standards, but to first understand staff and material flows and operational needs, and then work USP standards around these ideal flows. Having the users involved throughout the design process will ensure that appropriate flows and processes are maintained. Staff will also need to be compliant with USP 800 operational requirements, so they should be well-versed on the regulations from the pharmacist perspective as well.
One of the first things to discuss with the users is which aspect(s) of compounding will be performed at their facility. Is there an operational plan to compound all four aspects from day one or accommodate additional aspects in the future? Staff flow, operations, quantities and types of drugs, and future expansion are all design considerations that need to be thoroughly understood in order to create the best and most efficient plan for the current facility use, as well as potential future uses. Different facilities can compound the same type of drugs or have the same type of buffer rooms but utilize different workflows. This, in turn, creates different needs for number of anterooms, buffer rooms, storage, and receiving rooms. The most common concept plan for accommodation of USP 800 is for a non-HD buffer room and HD buffer room to share one anteroom with an HD storage room next to the HD buffer room with a pass-through between the two rooms to minimize transfer distance and potential spills and contamination, as shown in the diagram below.
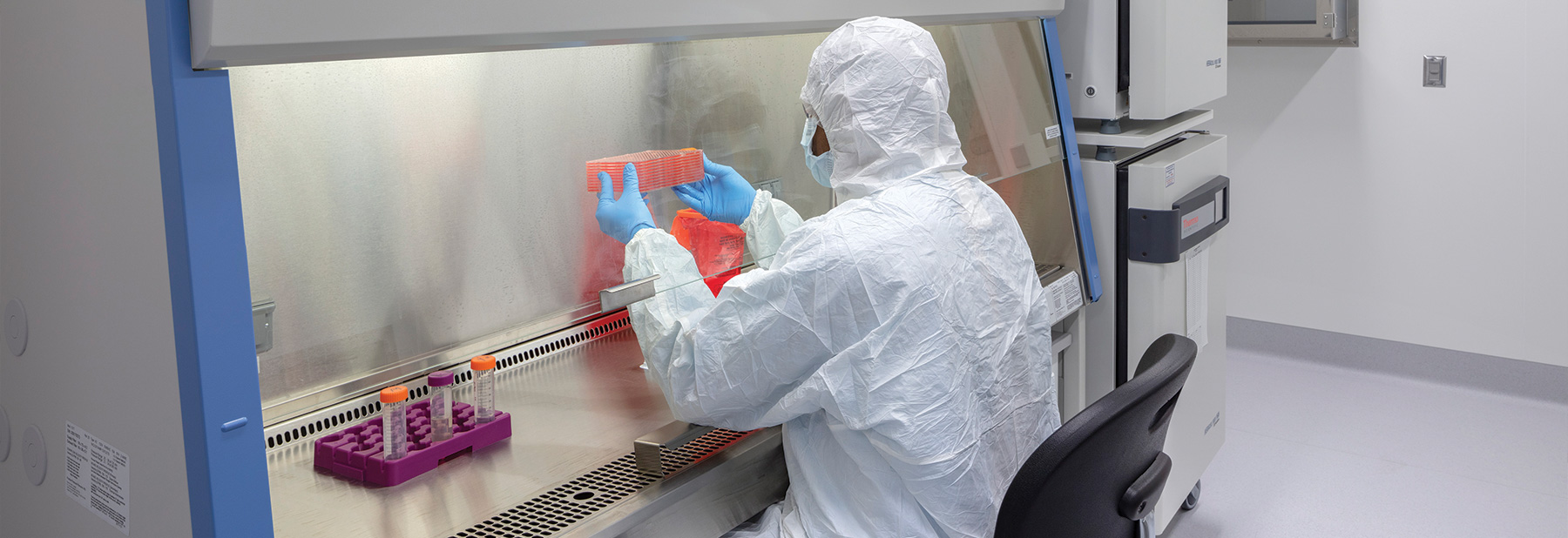
Key Design FactorsWithout diving into all the requirements of USP 800, the following are several additional key factors to consider in designing compounding pharmacies:
Staff working in buffer rooms can feel isolated since they should limit frequency of entry and exit to minimize gowning and de-gowning and maintain desired room pressurization and airflow. This can be mitigated by adding large interior glass windows wherever feasible and installing an intercom system; however, it is not recommended to include exterior windows within cleanrooms, as this creates additional challenges, such as managing temperature and humidity levels.
The location of the compounding pharmacy within a multilevel tower should correspond with hospital workflows, as well as mechanical access. The HD buffer rooms are required to be externally vented; therefore, planners need to factor this into their design early in the process to ensure, for example, that exhaust ductwork potentially containing HD particulates are not routed vertically through multiple floors or discharged adjacent to exterior public spaces.
This leads to possibly the most important element in keeping the pharmacy design USP 800 compliant – the HVAC design. The ISO classification required for aseptic cleanrooms depends on a well-planned HVAC design. The mechanical engineers should have pharmacy design experience and a thorough understanding of the environmental and ventilation requirements contained in all USP Chapters. Designers and planners should utilize these engineers as a resource to understand elements such as room pressurization and air changes to plan the most efficient layout (whether stick-built or modular turnkey system). Pharmacy cleanroom vendors are also available as consultants to designers and/or clients. Since pharmacy cleanrooms are complicated and often left to the designer's individual interpretations, it is beneficial to work with an experienced cleanroom vendor. Many of these vendors guarantee USP compliance in their service and provide continuing services and maintenance to the facility.
Even though there are many challenges that USP compliance presents, the result of successfully adhering to these standards results in improved safety for pharmacy and other hospital staff. By fully complying with applicable USP Chapters, designers can be assured that they have developed a safe workplace for those handling these life-saving drugs.
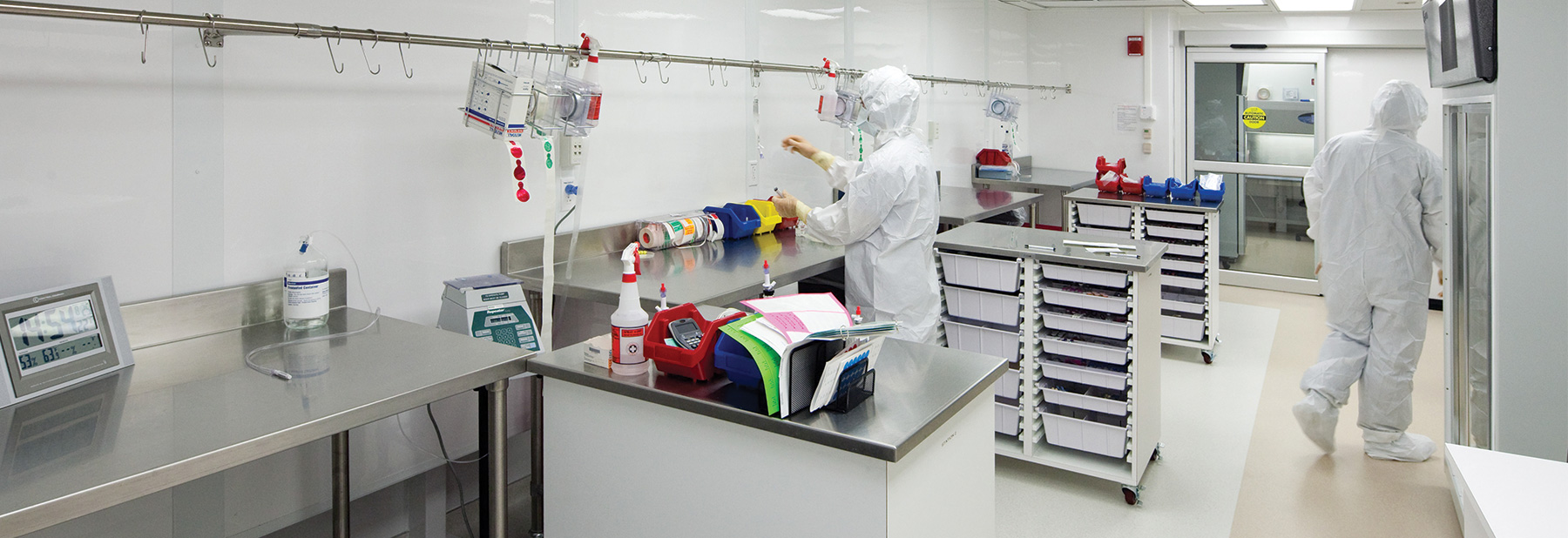